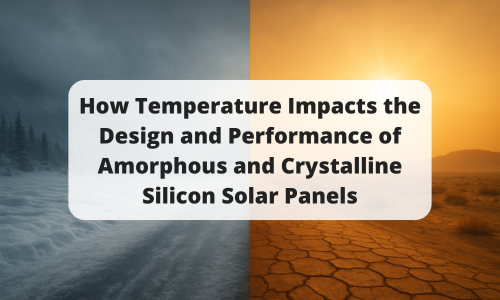
Temperature affects more than just power output—it influences reliability, material stability, and system longevity. For teams integrating solar energy into individual products or complex systems, understanding how heat and cold affect panel behavior is essential for making informed design choices.
This guide focuses on amorphous and crystalline silicon solar technologies. We’ll break down the impact of temperature on encapsulation, photovoltaic power output, and overall system performance. You’ll also see how thoughtful design helps mitigate temperature-related risks in real-world deployments.
Temperature Plays a Key Role in Solar System Design
.jpg?width=300&height=200&name=Design%20Proactively%20for%20Thermal%20Challenges%20(Web).jpg)
When you build a solar-powered solution, you need more than sunlight—you need the right thermal environment. Heat can degrade efficiency and materials, while cold can cause mechanical stress. By understanding how your system behaves across temperature extremes, you can design for performance and longevity.
Take this blog post with you!
Encapsulation Materials Impact Thermal Endurance
.jpg?width=300&height=189&name=Encapsulation%20Materials%20Impact%20Thermal%20Endurance%20(Web).jpg)
Encapsulation shields solar cells from ultraviolet (UV) rays, heat, and humidity.
At PowerFilm, we use Thermoplastic Polyurethane (TPU) or Ethylene-vinyl acetate (EVA), paired with an Ethylene tetrafluoroethylene (ETFE) top film, in all outdoor-rated panels.
This durable encapsulation stack:
- Blocks UV radiation
- Resists thermal cycling
- Prolongs system lifespan
When thermal reliability is a concern, low-cost encapsulation options can lead to early degradation and costly failures. We select materials that match the environmental requirements of your solution.
Learn more about why encapsulation matters.
Color Can Influence System Temperature
.jpg?width=300&height=200&name=Color%20Can%20Influence%20System%20Temperature%20(Web).jpg)
Color has a limited effect on solar panel efficiency, but it can influence system temperature. Darker materials in non-active areas—such as borders or housing—absorb more heat, though this has minimal impact on the solar cells themselves.
However, color plays a larger role when you integrate electronics into your system.
For example, several PowerFilm panels include charge controllers with power electronics that rely on their enclosures for cooling. Reducing the thermal load from sunlight can improve power handling. In these cases, we often use white housings instead of black to reflect sunlight and reduce heat absorption.
This thermal management strategy enhances controller performance in direct sunlight and extends system lifespan.
Temperature Coefficients Define Performance in Heat
.jpg?width=300&height=200&name=Temperature%20Coefficients%20Define%20Performance%20in%20Heat%20(Web).jpg)
Solar panel efficiency changes as temperatures rise or fall. The temperature coefficient tells you how much output a panel loses per degree above 25°C.
The lower the coefficient, the better a panel maintains its output in hot conditions:
- Low-cost crystalline silicon panels lose 0.40% per °C.
- PowerFilm Maxeon crystalline panels lose 0.29% per °C.
- Amorphous silicon panels lose 0.16% per °C.
If your solution must perform in sustained heat, both amorphous and Maxeon crystalline technologies provide strong thermal resilience, reducing degradation and supporting long-term efficiency. Learn how Maxeon delivers real-world benefits in our full overview of Maxeon’s thermal performance.
Know the Ideal Operating Temperature Range
.jpg?width=300&height=161&name=Know%20the%20Ideal%20Operating%20Temperature%20Range%20(Web).jpg)
Each panel technology performs best within a specific temperature range.
PowerFilm amorphous panels operate from -40°C to 85°C, with optimal performance between 25°C and 50°C. We guarantee reliable operation in standard atmospheric conditions up to 85°C.
Crystalline silicon panels perform best in cooler temperatures but lose efficiency as heat increases. Maxeon panels offer a lower temperature coefficient than other crystalline options, maintaining higher output in hot conditions.
Test in the Environment Where the System Will Run
.jpg?width=200&height=133&name=Varrying%20Operating%20Environments%20(Web).jpg)
.jpg?width=200&height=133&name=Solar%20Operation%20In%20Different%20Seasons%20(Web).jpg)
Lab tests provide helpful baseline data, but real-world testing is crucial for understanding how your system responds to temperature changes, varying light conditions, and seasonal fluctuations.
Keep these key points in mind:
- Test in the actual deployment environment whenever possible.
- Match the test duration to your deployment length. A summer-only test won’t prepare your system for winter performance.
- Understand the Staebler-Wronski Effect, which temporarily reduces output in amorphous silicon panels. Summer heat helps panels self-repair (anneal), while winter slows the recovery process.
- Crystalline panels typically perform better in cooler conditions but lose efficiency more rapidly in high heat.
If your test plan overlooks these variables, your system may underperform or fail once seasonal conditions shift.
Design Proactively for Thermal Challenges
%20(Web).jpg?width=300&height=200&name=Design%20Proactively%20for%20Thermal%20Challenges%20(2)%20(Web).jpg)
Every solar-powered product must contend with heat and cold. When you plan ahead, select the right materials, and test under real conditions, you reduce risk and build a system that performs reliably for years.
At PowerFilm, we collaborate closely with engineers and product teams to design solar solutions that perform optimally in their operating environments. Our team helps you choose the right materials, validate your design, and ensure consistent performance across a wide range of temperatures.
Ready to design a solar solution that performs in any environment?
Contact us today to start your next project.
Related Resources
Looking for more information on designing durable solar solutions? Explore these helpful guides:
Take this blog post with you!